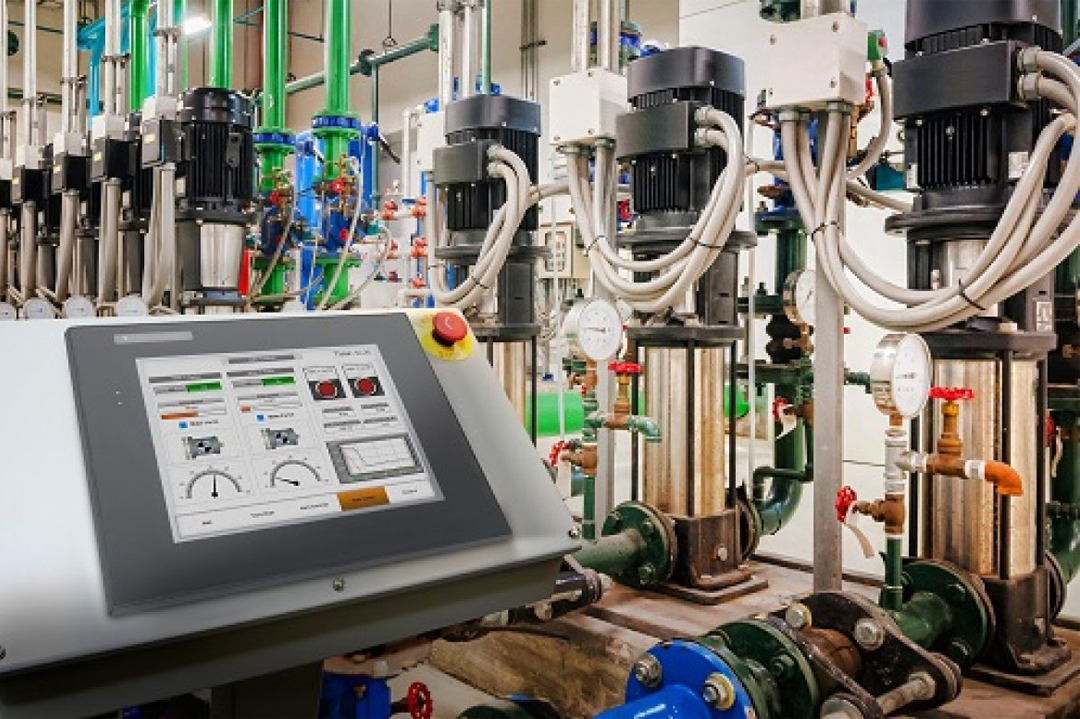
مقدمه
محیطهای صنعتی مختلف نظیر پالایشگاهها، نیروگاهها، کارخانجات فولاد وغیره نیازهای بیشمار جوامع را تولید میکنند. در هر کدام از این محیطهای صنعتی، غالبا فرایندهای پیچیده و بزرگی انجام میشود. در تمام این فرایندها برای اطمینان از عملکرد مناسب و صحیح پروسه نیاز است تا اطلاعاتی از جریان فرایند، از قبیل دما، فشار نقاط مختلف و همچنین فلوی عبوری از نقاط خاص و وضعیت مخازن و غیره به طور دقیق در هر زمان در دسترس باشد. با استفاده از این اطلاعات سیستم کنترل قادر خواهد بود پروسه را جهت دستیابی به محصول مورد نظر هدایت نماید. فرایند اتفاق افتاده در این قبیل پروسهها همواره با تغیرات پیوسته شیمیایی همراه است یعنی فرایند نیازمند کنترل مداوم پارامترهای آن میباشد. این پروسهها دارای حلقههای کنترلی متعددی میباشند که امروزه مناسبترین روش برای کنترل آنها سیستمهای DCS[1] میباشد که لوپهای کنترلی را در CPU های مستقلی پردازش میکند. در این مقاله سعی در معرفی کلی شبکه های کنترل و اتوماسیون در پروسه های صنعتی شده است.
سیستم کنترل
یک سیستم کنترل که قابلیت تنظیم مقدار خروجی سیستم را متناسب با ورودی اعمالی به کنترلر را داشته باشد، میبایست در هر لحظه توسط سنسورها از مقدار خروجی نمونه برداری کند. این مقدار سپس با مقدار ورودی یا مقدار مطلوب کمیت مقایسه شده و سیگنال خطا را ایجاد میکند. برای ایجاد این سیگنال میبایست سیستم به صورت فیدبک منفی بسته شده باشد. سیگنال خطا به عنوان ورودی به سیستم کنترل اعمال شده و کنترلر با توجه به مقدار انحراف کمیت تنظیمات لازم را روی عملگر انجام میدهد. اجزای تشکیل دهنده سیتم کنترل حلقه بسته فیدبک منفی در زیر اشاره شده است:
1- پروسس
منظور از پروسس یا فرایند سیستم یا مجموعه المانهایی است که از یک طرف مواد به آنها وارد، و پس از اعمال تغییرات فیزیکی و شیمیایی از آن خارج میشود.
2- تجهیزات ابزار دقیق
منظور تجهیزاتی است که به منظور اندازهگیری کمیتهای پروسه نظیر دما، فشار، فلو ، سطح و غیره استفاده میشوند و به عنوان المان اولیه یا حسگرمورد استفاده قرار میگیرند.
3- ترنسمیتر
مقدار اندازهگیری شده توسط تجهیزات ابزار دقیق میبایست قبل از ارسال به کنترلکننده تقویت شده و مدولاسیون مناسب جهت ارسال اعمال شود .
4- مقایسه کننده
خروجی اندازهگیری شده پروسه میبایستی با مقدار مطلوب مقایسه گردد تا در صورت وجود خطا، تدابیر لازم بکار گرفته شود. عمل مقایسه در قسمت مقایسه کننده انجام میپذیرد.
5- کنترل کننده
کنترلکنندهها یکی از قسمتهای مهم و حساس سیستمهای کنترل صنعتی میباشند و طراحی و تنظیم آنها از اهمیت و حساسیت ویژهای برخوردار است.کنترلکنندهها سیگنال خطا را دریافت نموده و با توجه به تنظیمات انجام شده قبلی فرمانی را صادر میکنند و این فرمان توسط قسمتهای بعدی اجرا میشود کنترلرهای صنعتی امروزه معمولا مبتنی بر کنترلرهای PID میباشند. در این نوع کنترلرها ضرایب توسط طراح تعیین میشود. ضریب P سرعت تغییرات را در خروجی سیستم را تعیین میکند اما افزایش زیاد آن باعث ایجاد خطا در سیستم خواهد شد. ضریب I چون از سیستم انتگرالگیری میکند باعث از بین رفتن خطای حالت ماندگار سیستم شده و تغییرات در خروجی را نرمتر میکند. ضریب D چون از سیستم مشتق میگیرد حساسیت سیستم را نسبت به تغییرات ورودی افزایش میهد.
6- تقویت کننده
فرمان ارسالی از کنترلکننده قبل از انتقال به عملگر میبایست تقویت شود.
7- محرک
چون سیگنال کنترلی که از طرف کنترلکننده به سایت ارسال میشود قدرت لازم جهت حرکت دادن عنصر نهایی را ندارد، از محرک استفاده میشود.
8- عنصر نهایی
همانگونه که از نامش پیداست آخرین قسمت سیستم کنترل میباشد و ورودی از طریق آن به پروسه اعمال میشود. در فرایندهای صنعتی معروفترین عنصر نهایی شیرها میباشند.
بلوک دیاگرام نشان داده شده در شکل1 نمایشی کلی از سیستمهای کنترل صنعتی میباشد:
شکل 1 کنترلر حلقه بسته با فیدبک منفی
در این سیستم کنترل که هدف رسیدن پروسه به نقطه مطلوب[1] است در هر لحظه مقدار کمیت مورد نظر توسط حسگر اندازهگیری میشود. حسگر متناسب با تغیرات کمیت، سیگنالی را تولید میکند، مبدل حالت آن را در صورت لزوم به سیگنال ولتاژ یا جریان تبدیل میکند. این سیگنال چون میبایست با مقدار مطلوب مقایسه شود خطیسازی شده و نویزهای آن فیلتر میشود. در بسیاری مواقع چون فاصله حسگر و کنترلکننده زیاد میباشد، سیگنال باید تقویت و ارسال شود. این سیگنال با سیگنال مرجع مقایسه شده و تفاضل آنها سیگنال خطا نامیده میشود. سیگنال خطا به عنوان ورودی به کنترلکننده اعمال میشود. کنترلر با توجه به منطق برنامه سعی در تنظیم خطا خواهد داشت. سیگنال خروجی از کنترلر پس از تقویت به عملگر مناسب اعمال شده و در نتیجه پروسه در نقطه مطلوب تنظیم میشود. این سیستم یک سیستم کنترل حلقه بسته نامیده میشود که برای تمامی پارامترهای تحت کنترل میبایست تشکیل شود. با توجه به اهمیت این موضوع در مورد پروسههای پیچیده نظیر صنایع پتروشیمی و احیای فولاد این سیستم میبایست قابلیت تحلیل و کنترل حلقههای متعدد و وابسته بهم را داشته باشد. علاوه بر آن میبایست در صورت بروز هر گونه اشکالی از کار نیفتاده و یا به اصطلاح سیستم به صورت افزونه[2] طراحی شده باشد.
سیستمهای کنترل توزیع شده (DCS)
با معرفی پروسسورها و میکروکنترلرها، کنترل و پردازش قسمت های مختلف پروسه بین کنترل کننده ها تقسیم شد و باعث به وجود آمدن نسلی از روش کنترل به نام DCS (Distributed Control System) به معنی سیستم کنترل توزیع شده است. این سیستم غیر متمرکز بوده و کنترل توسط چند کنترل کننده که در اتاق کنترل قرار گرفته اند صورت می پذیرد. یکDCS مجموعهای است از کنترلرهایی با قابلیت پردازش بیش از یک حلقه (Multi-Loop). این کنترلرها که با یکدیگر نیز مرتبط بوده و قابلیت کنترل صدها حلقه را دارا میباشند. در یک پروسه تولید اطلاعات فیلد از قبیل دما، فشار، جریان و غیره توسط تجهیزات ابزار دقیق به شکل سیگنال استاندارد جریان یا ولتاژ تبدیل و مدوله شده و آماده ارسال به قسمت I/O سیستم DCS می شود.برای ارتباط سیستم I/O و کنترلر به دلیل حجم بالای اطلاعات از سیستم پروفیباس استفاده می شود. پس از پردازش اطلاعات و صدور فرامین کنترلی بر اساس نیاز فرایند این سیگنال دوباره به قسمت I/O فرستاده میشود و از آنجا به عملگرهای الکترومکانیکی برای تنظیم پارامترهای مورد بررسی ارسال میگردد.
معماری سامانههای DCS
سامانههای DCS از نظر تجهیزات و خطوط ارتباطی بین آنها در سه لایه قابل تشریح میباشد که در زیر بصورت هرمی نمایش داده شده است.
1- Field Level
2- Control Level
3- Monitoring Level
شکل2 هرم اتوماسیون
Field Level
در پایین ترین سطح Actuator ها و Field Instrument ها قرار دارند که می توانند به روش کلاسیک یعنی ارتباط از طریق دو رشته سیم (جریان یا ولتاژ) و یا به روش Field bus به کارت های I/O متصل شوند. امروزه از تکنولوژی Field bus جهت این ارتباط استفاده می شود. حجم دیتا در این سطح کم است ولی زمان ارسال و دریافت اطلاعات باید کوتاه و در حد میلی ثانیه باشد. ارتباط از نوع پروفیباس H1 در سطح فیلد ایجاد و سرعت تبادل اطلاعات در آن معادل Kbit/S 31.25 میباشد. ادوات نصب شده به این باس انرژی الکتریکی تغذیه خود را از باس و ارتباطات آن دریافت مینمایند. با استفاده از تکنولوژی فیلدباس میتوان از توپولوژیهای مختلف نظیر Tree ، Star و... استفاده کرد.
Control Level
در سطح میانی یک سیستم DCS کنترلر ها قرار دارند. هر کنترلر متصدی اداره یک قسمت از Plant است و معمولا به همین شکل نیز نامگذاری می شود. کنترلر ها از طریق یک شبکه ارتباطی با یکدیگر و نیز با سطح بالاتر در ارتباط هستند. از این شبکه نیز معمولا تحت عنوان Process Bus یاد میشود. این شبکه معمولا دارای پشتیبان Redundant است. حجم دیتا نیز در این کم و در حد بایت است و زمان تبادل نیز باید کوتاه و کمتر از ثانیه باشد.
Monitoring Level
در سطح بالای یک سیستم DCS ایستگاه های کاری یا همان کامپیوترهایی قرار دارند که از طریق آنها فرایندهای پروسسی توسط اپراتورها کنترل میشوند. این کامپیوترها نیز از طریق یک شبکه که به آن Terminal Bus گفته میشود به سطح پایینتر متصل میشوند. حجم اطلاعات در حد متوسط و زمان نیز در حد ثانیه است.
شکل 3 معماری یک شبکه متعارف DCS
همانگونه که در شکل مشاهده می شود در این سطح Engineering Station قرار میگیرد که نرم افزار طراحی و مهندسی سیستم DCS روی آن نصب میشود و کلیه عملیات مهندسی شامل download کردن برنامه ، تغییر در منطق برنامه و تغییرات در صفحات گرافیکی سیستم از طریق آن صورت میپذیرد. ES به هر دو Bus سیستم اعم از terminal Bus و process Bus متصل است.
OS یا Operation Station همان ایستگاه کاری اپراتور هاست. در این قسمت صفحات گرافیکی به شکل Runtime و غیر قابل تغییر است بار گذاری شده است. OS ها بسته به معماری سیستم به صورت مستقیم یا از طریق Server به کنترلر ها متصل هستند. اپراتورها می توانند مقادیر پروسسی را روی OS مشاهده نمایند و یا فرامین کنترلی را از طریق آنها به کنترلرها ارسال کنند.
DCS های مطرح دنیا
سازندگان مختلفی که البته تعداد آنها زیاد نیست سیستم های DCS را ارائه کرده اند. برخی از DCS های معروف عبارتند از:
Centum 3000 ساخت شرکت YOKOGAWA
Delta V ساخت شرکت EMERSON
Industrial IT ساخت شرکت ABB
Teleperm XP ساخت شرکت SIEMENS
PCS7 ساخت شرکت SIEMENS
Experion PKS ساخت شرکت Honeywell
نتیجه گیری
با توجه به اهمیت بهینه سازی و تولید محصول با کیفیت و همچنین حصول حداکثر ایمنی در پروژه های صنعتی لزوم استفاده از کنترل کننده های با دقت بالا بیش از پیش احساس می شود. سیستم های مبتنی بر DCS به دلیل برخورداری از نرم افزار و سخت افزار قدرتمند قابلیت کنترل دقیق و مونیتور کردن پروسه را دارا بوده وامکان تصمیم گیری راحت را برای اپراتور فراهم میسازد.
Lessons In Industrial Instrumentation, By Tony R.Kuphaldt , Version 1.14
Instrument Engineers’ Handbook – Process Control Volume II, Third Edition,
Moore 353 Process Automation Controller User’s Manual”, document UM353-1, Revision 11
Process Control Fundamentals , http://www.pacontrol.com
WWW.ABB/Process Control.com
WWW.Siemens/Process Control.com
هیچ دیدگاهی برای این مطلب ثبت نشده است.